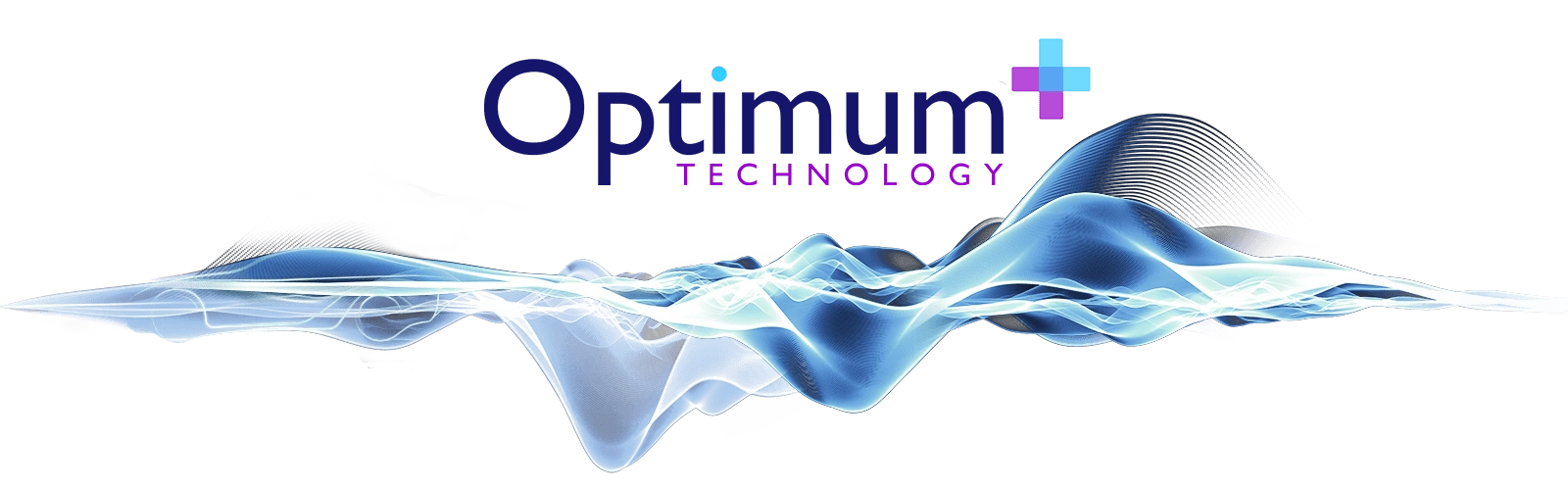
Ultra lightweight, highly absorbent, fluff pulp free, adhesive and binder free, core wrap free, low cost absorbent cores of less than 2mm in thickness.
Suitable for incorporation into Infant Diapers, Adult Incontinence, Feminine Hygiene products and other applications where liquid absorption is required.
These absorbent cores are produced using sound waves to dissipate powdered or spherical grades of Sodium Polyacrylate blends of any commercial type or PSD within a single layer, application specific nonwoven fabric substrate that functions as the core.
This innovative absorbent system also incorporates a new, in house developed Acquisition and Distribution Layer (ADL) that also functions as a Top Sheet providing exceptional softness, comfort and performance for the consumer.
Our new cores have been independently tested in accordance with EDANA and INDA protocols providing results that outperform all of the global market leading brands.
Used for the manufacture of ostomy products, the film is virtually silent in use, does not require a separate activated carbon filter to control flatus gases and can be manufactured in rotary production systems to achieve higher output speeds with smaller machine footprint.
The film can be manufactured from wholly bio sourced materials if required.
Produced using our new, dry dissipation technology using sound waves at up to 10x faster production speeds when compared to conventional wet spray production systems.
Suitable for the manufacture of wound care dressings, CBRN protection systems, medical filtration and many other gas and odour filtration applications.
We have developed a novel process for managing, impregnating and immobilising powders and particles within air permeable substrates using sound waves only without the use of binders, adhesives or any other bonding agents whatsoever.
This technology is fast, effective and highly energy efficient and can be applied to most powder types and particle sizes.
We also have the resources to develop, produce and test application specific substrates for virtually any given product type or structure thereby ensuring optimum performance of the end product at the lowest manufacturing cost.
We have developed a novel process for managing, impregnating and immobilising powders and particles within air permeable substrates using sound waves only without the use of binders, adhesives or any other bonding agents whatsoever.
This technology is fast, effective and highly energy efficient and can be applied to most powder types and particle sizes.
We also have the resources to develop, produce and test application specific substrates for virtually any given product type or structure thereby ensuring optimum performance of the end product at the lowest manufacturing cost.
Powders consist of three basic phases:
Generally, powders with an average particle size below 10 microns have poor flowability and can therefore be difficult to process in product manufacture.
We have developed a technology to ensure that even the most nonflowing powder types can be made to flow readily without additives or lubricants of any type.
These powders can then be very accurately dispersed onto the substrate surface and impregnated into the substrate using our sound wave technology.
We have developed a technology for immobilising impregnated powders within a given substrate without the use of binders or adhesives thus ensuring that the powders are able to function at maximum efficiency.
This technology uses the structure of the substrate itself to entrap the powder within the substrate matrix and can be applied to most powder and particle types irrespective of the particle size distribution profile of the powder.
Optimum Technology provides established Tier 1 and Tier 2 partners in each market sector of Healthcare, Hygiene, Cosmetics, Wound Care and Energy Storage with technology and service solutions under own label manufacturing, marketing and sales agreements, technology or product licensing agreements, technology transfer arrangements or joint ventures.
As a business, we have key strategic relationships with global leaders in biodegradable materials, technical non woven fabrics, state of the art manufacturing, engineering tooling, production systems, advanced processing and robotics in addition to close working relationships with world class research and development houses on three continents and Tier 1 universities.
We have developed key skills and expertise in the sourcing, implementation and processing of biodegradable and fibre based materials obtained from sustainable and renewable resources into new, high performance technologies that provide not only green solutions in terms of disposal but importantly further improve the lives of consumers and patients.
A key aspect of our activity is the development of new technology and new products with genuine commercial potential. We are constantly looking to develop disruptive technologies and we invest heavily each year in such programmes with at least 30% of our annual revenues being earmarked for internal research and development.
We operate in the global market and have representation in the Americas, all over Europe and Asia. Together with our network of specialists and experts in local, regional and international markets we are able to take on any challenge from one off R&D projects to full scale product, process and manufacturing development.
Although we generate our own innovative products and design concepts in-house, we are always open to collaboration with other companies, universities and experienced inventors so if you feel that we have the resources and expertise necessary to assist your project, please contact us.
We have developed and own a new technology for use in the manufacture of consumer hygiene products that produces absorbent cores that are extremely thin and contain no fluff pulp or adhesive materials within the core construction. This absorbent core technology is suitable for use in the manufacture of infant diapers, adult incontinence products and feminine hygiene products as well as ancillary products such as absorbent bedding, absorbent seating covers and any other relevant application where liquid waste requires an absorbent media.
We are working closely with a major global player in the wound care market to develop an improved wound care dressing for use on patients with acute, chronic or second and third-degree burns. The new dressing will evacuate fluid from the wound bed and increase blood flow to the area thereby improving healing time and outcomes. Using a variation of this new wound care dressing type, it will also be possible to irrigate to wound and or supply remedials such as anti-biotics directly to the sire of the wound.
In conjunction with a global leader in the cosmetics industry, we are developing a new technology to impregnate active powders into cellulose based non-woven fabric substrates to create a new generation of skin care products. These new products will be more efficient at delivering the active powder to the skin and also result in the need for simpler packaging which can either be fully recyclable or biodegradable.
We have developed and own a new technology that provides an alternative to the use of PVdC, PVOH or Nylon as a gas or odour barrier in thin films & foils whereby we adsorb the contained gases or odours within a sandwich structure. This technology has particularly useful applications in devices used for the collection of body waste such as in ostomy, urostomy and ileostomy pouches since the technology allows for the elimination of a separate conventional activated carbon filter within the product for providing odour control to flatus gases. The elimination of a separate filter structure also allows for the pouches to be manufactured in a rotary production system thereby making manufacture both faster and less expensive than current indexing manufacturing systems.
Conventional battery technology broadly falls into two sectors – acid cell or Lithium ion technology. Lithium ion batteries are the current choice for portable devices such as mobile phones and laptops as well as fully electric and hybrid cars. The main problem with batteries used for propulsion in electric vehicles is range anxiety and charging time. These two issues revolve around the energy storage density of the battery itself. At this time, the effective range of Lithium ion batteries in cars is around 300 miles (480 Km) and those batteries provide circa. 85kWh and weigh upwards of 500Kg – this equates to 1kWh per 6.35Kg of battery. Our focus is to drastically improve the power to weight output of battery technology by using carbon based technology and without Lithium. Lithium is a finite resource that is expensive, hazardous and prone to fire as has been the case with some electric vehicles and mobile devices. Carbon is an abundant resource that is cheap, safe and easy to process and handle. Our target is to achieve energy storage at 1kWh per 1kg of battery – thus making a single charge range of 1000 miles possible with very fast charging times. We are also working on carbon based technology for a new type of supercapacitor to enhance the use of our new battery technology within the vehicle propulsion sector.
We have developed and own a new technology for managing the dissipation of activated carbon within breathable substrates and fibrous structures in a wholly dry process. Our process is more than 10x faster than conventional wet spray methods and provides structures suitable for use in the manufacture of wound care dressings, CBRN protective systems, medical and other filtration devices in addition to super capacitor applications for energy recovery and storage systems.
24 Grosvenor Street, West End, London, W1K 4QW, United Kingdom
Telephone: +44 (0)207 491 1810 group@optimum-technology.com
CORPORATE OFFICE
22 Athol Street, Douglas, Isle of Man, IM1 1JA
Telephone: +44 (0)16 246 756 10
We are fully compliant with the European General Data Protection Regulation (GDPR) of 25 May 2018. Although we may hold Personal Data (as defined within the regulation) about you, for example, your name, telephone number and/or email address, we do not hold any Sensitive Personal Data (as defined within the regulation) about you or any other of our commercial or business contacts whatsoever. We never share any Personal Data that we hold about any of our commercial or business partners or contacts. If you require any further information or questions about how we manage personal data within our organisation, please contact our Processor at
Copyright © 2024 Optimum Technology - All Rights Reserved
www.optimum-technology.com